Chapter Five: Hydraulic Press Processes
Since the development of the Bramah Hydraulic Press at the end of the 18th Century, the hydraulic press has rapidly improved and advanced to become a highly technical tool that can provide precision and accurate deforming of materials. The pressurized compressive force of a hydraulic press is an essential part of metal deforming and shaping.
There is a wide array of deforming and shaping methods that a hydraulic press is able to perform. Each of the various processes perfectly manipulates a workpiece to match the requirements of a product or design.
Hydraulic Press Processes
When a hydraulic press is being used to cut, bend, form, draw, punch, coin, or pierce a workpiece, it becomes a means of forging the workpiece using a die with an upper and lower half the shape and form of the piece to be produced. The workpiece is placed on the lower half of the die and the ram lowers the upper half to compress the workpiece to create the desired shape.
Blanking
Blanking is a process of cutting a shape or form from a coil, sheet, strip, or billet of metal. The cut shape is sent on to be further processed. The most common form of blanking is done with a coil of metal that is fed into a hydraulic press.
In the image below, the coil enters on the right, the shape is cut, and it can be seen on the left.
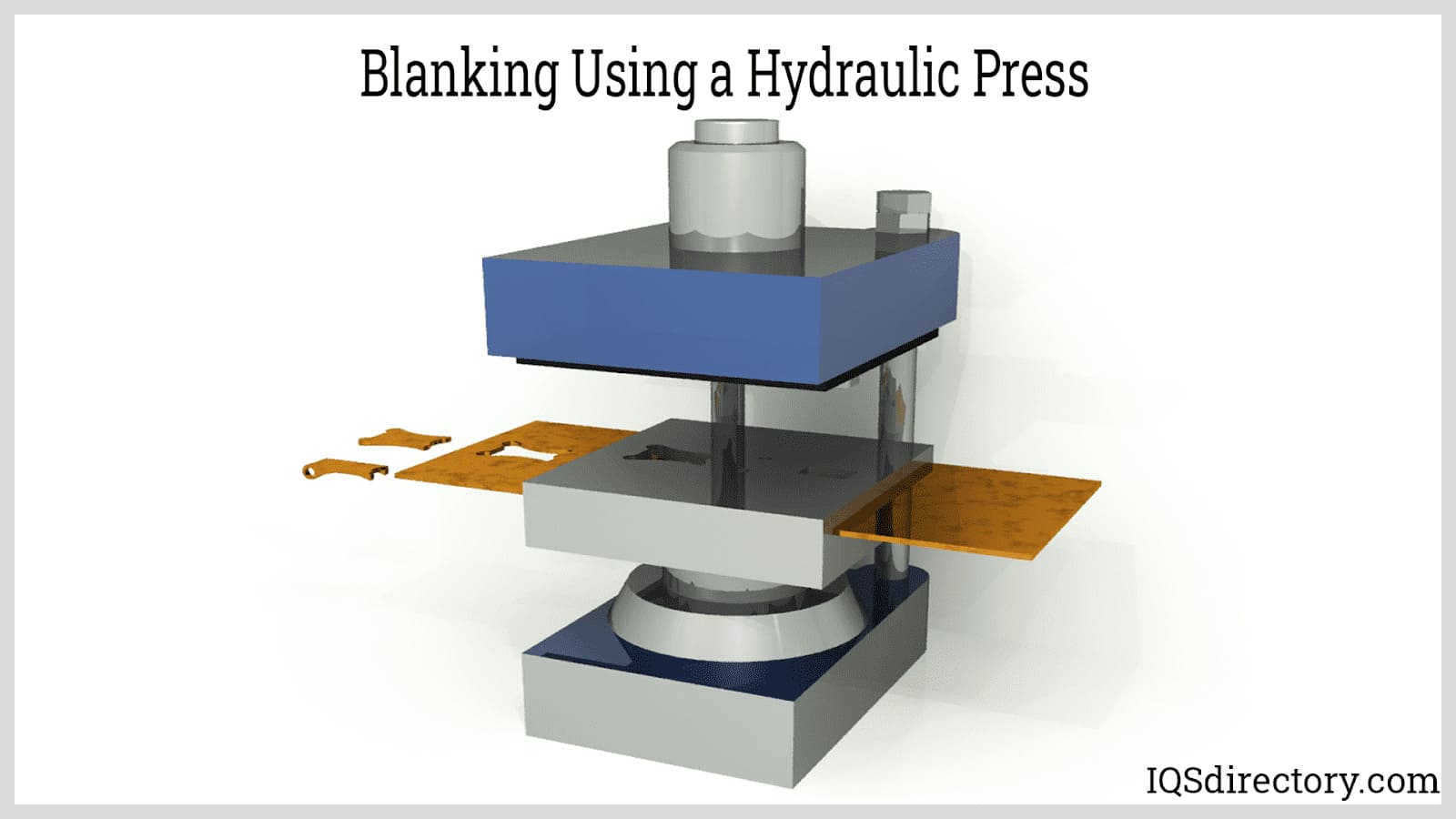
Drawing
Metal drawing deforms a workpiece by reducing its cross section using a mold or die that has a smaller cross sectional area. Unlike extrusion, where the workpiece is pushed through a die, in the drawing process, the workpiece is pulled through the die. The completion of drawing can require force as high as 150 tons.
Piercing
Piercing is a sheet metal punching process that is used to extrude shapes in a metal sheet. The term piercing is a generic term used to describe the cutting, punching, and shearing of openings in a workpiece. Piercings can be holes, slits, slots, or any other shape, and it is the opposite of blanking. In the blanking process, the piece that is cut out is the workpiece. In piercing, the section that is cut out is scrap.
In the image below, the finished product on the left has had the scrap on the right removed by piercing.
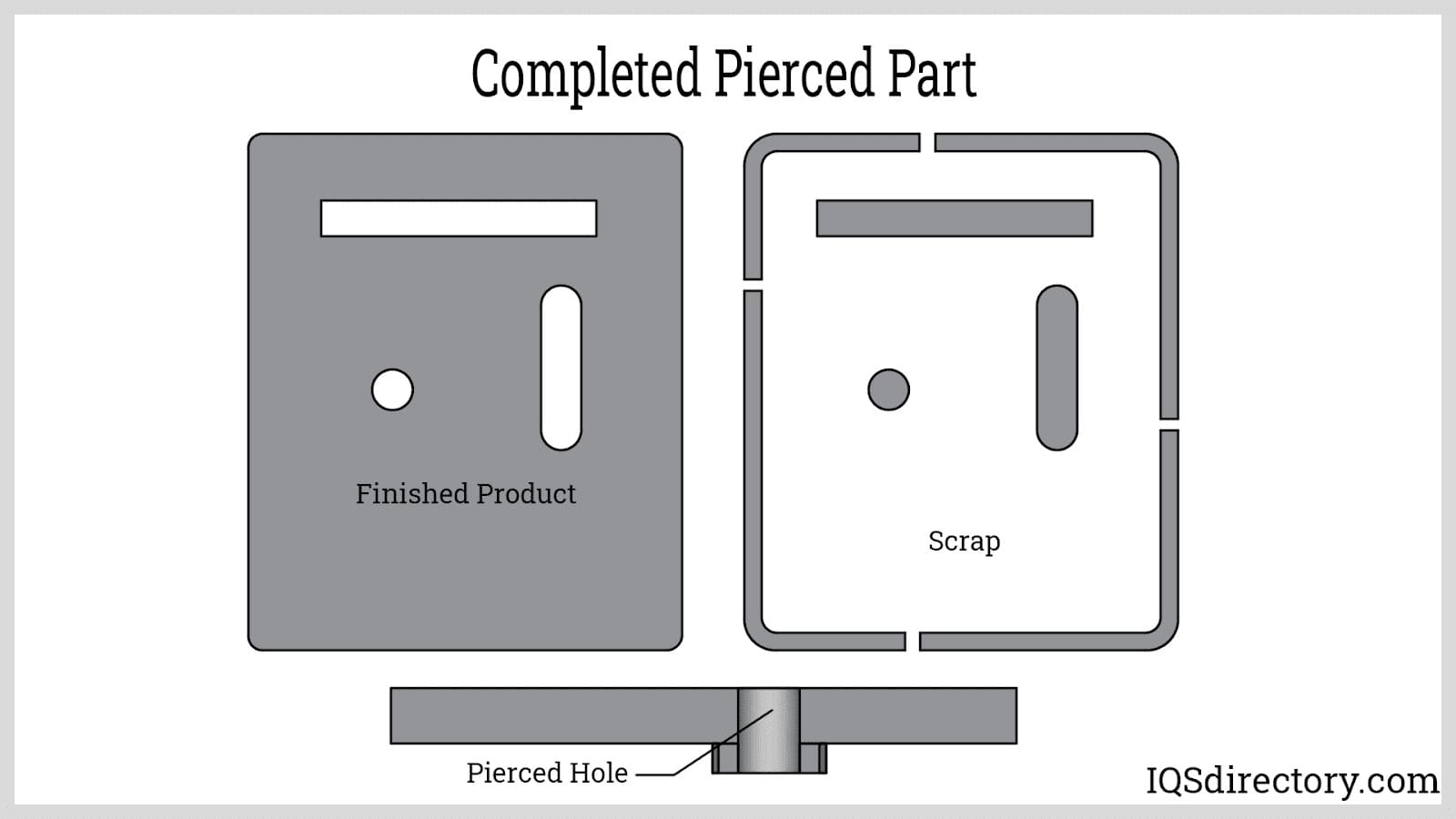
Stretching
A major concern for government monitoring agencies is the amount of noise that employees are exposed to during their work day. Excessive noise can result in serious medical and mental issues that lead to absenteeism and production down time. Since a hydraulic press does not have any moving parts, its operation noise level is significantly reduced. The precision control provided by a hydraulic press allows management to control the amount of noise it will produce.
Upfront Costs
Another aspect of the mechanical operation of a hydraulic press is the cost of purchasing it. Without the need for machining or mechanical parts, a hydraulic press is less expensive to purchase and takes less time to set up. The simplicity of its operating process becomes economically apparent on the day it is installed.
Range of Designs
From hand operated hydraulic presses to those of several tons, there is a hydraulic press to fit any application or operation. Sales staff and manufacturers work closely with their clients to develop a metal working process that fits the needs of any application. There are table top models for laboratories and massive hydraulic presses that apply hundreds of tons of pressure. Regardless of the material to be shaped and formed, there is a hydraulic press to do the work.
Conclusion
- A hydraulic press is a mechanical device that uses the static pressure of a liquid, as defined by Pascal‘s principle, to shape, deform, and configure various types of metals, plastics, rubber, and wood.
- The passage of the fluids between the two pistons creates increased pressure that produces mechanical force to drive the anvil on a hydraulic press downward onto a workpiece that is deformed to produce a desired shape.
- The differences between the types of hydraulic presses depend on several factors, which include their frame and the metals used to manufacture them.
- From the shaping and creation of machine components to the crushing and compacting of waste and refuse, hydraulic presses are an essential part of modern industrial operations.
- Since the development of the Bramah Hydraulic Press at the end of the 18th Century, the hydraulic press has rapidly improved and advanced to become a highly technical tool that can provide precision and accurate deforming of materials.
No comments: